MAINTENANCE 411
It’s easy to forget about the water purification system in the corner of your basement, but it’s like anything else: if it doesn’t get the attention it needs, eventually it stops functioning like you want it to. Consider that the average household consumes 300 gallons of water per day. That’s thousands of gallons of water per year being processed through your water filtration system, making it the hardest working equipment in your home. Unfortunately, it’s often the most overlooked. Because water is such an important part of our lives, maintaining the system that transforms contaminated well water into safe, clean drinking water is crucial. You don’t realize just how much you rely on it until something goes wrong. Without routine annual maintenance, problems you thought were a thing of the past will return. Eventually this leads to even bigger problems that can result in costly repairs and even complete system failure. A simple annual service call can prevent this. Our service technicians have the knowledge and experience to troubleshoot, diagnose, and in most cases remedy any issues at the time of service, regardless of make or model. Because water is so vital to the health and wellbeing of you and your family, we believe in taking a pro-active approach to maintaining your water purification system. Adhering to our yearly maintenance program validates manufacturer’s warranties and ensures that your water continues to consistently provide you with a clean, safe water supply.
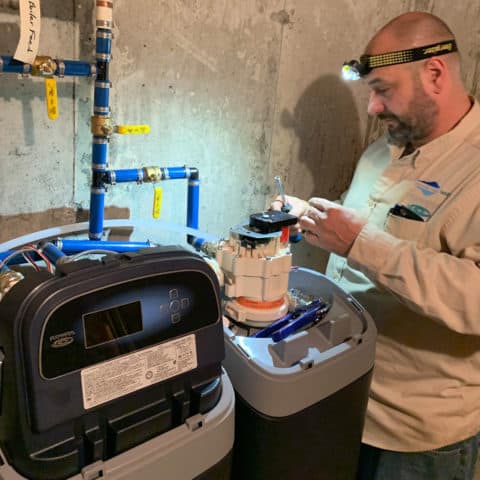
OUR GUARANTEE
We stand behind the products we carry and we stand behind the service we provide. An annual maintenance program with Summit View Water Ltd comes with our commitment to providing exceptional service to our customers. This means that if you’re experiencing problems with your water before you’re due for service, we’ll do everything possible to remedy the problem. If we can’t troubleshoot by phone, a technician can be dispatched at no charge. That’s our guarantee.
NEW HOME?
If you recently purchased a new home that has a water treatment system, you might be wondering what to do with it. Whether it was installed by us or by one of our competitors, we’re happy to schedule an appointment to service, repair, upgrade components, and in some cases replace your existing units.
If your new home has no water filtration system and you’re concerned about the quality of your water, we provide site inspections and water analysis to determine what further steps, if any, are necessary.
In either case, the most effective way to begin is with a current water quality report to determine the exact nature of your water. Because water chemistry can change over time, an outdated water quality report may not reflect the true quality of your water. You don’t want to treat for problems you don’t have, you want to treat the problems you do have. Contact Summit View Water, Ltd to get started.
MAINTENANCE PROGRAMS
Conditioners and Softeners
10-point Cleaning & Inspection: While your water softener doesn’t require a lot of attention to continue operating, an annual service plan will keep it running smoothly for years to come. Some of the steps your technician will perform during a 10-point cleaning and inspection include the following:
- Turn off water and depressurize unit
- Clean and inspect venturi assembly
- Check water usage, time of day, backwash and regeneration settings, making adjustments where necessary
- Inspect brine tank float valve assembly and drain line
- Inspect control valve, disks, o-rings and other moving parts for damage
- Remedy salt bridging or mushing
Water Filtration / Regeneration Systems
The basic components of a home water filtration system are a mineral tank and a control valve. The control valve is the brains of the system while the media (or resin) inside the mineral tank is what actually filters contaminants from the water. While the different types of media are more varied than the contaminants they’re used to treat, correct media application depends not only on the contaminants being treated but on backwash flow rate, service flow, tank size, water pressure, and other factors.
Backwashing filters trap and hold particles as water filters down through the resin bed. Over time, water creates paths through the media bed, reducing its exposure to the media and thus the effectiveness of filtration. This is called “channeling.” The process of backwashing cleans and resets the media resin by reversing the flow of water and sending it down a riser tube to the bottom of the tank. The force of the up-flow is such that it lifts the resin bed, dislodging particles and channeling before routing the contaminated water through the drain line. A rinse cycle then re-settles the resin bed for continued service.
Over the course of a year, any number of factors can influence this process, such as power outages, changes in water chemistry or water pressure, and reduced function of aging units. Minor adjustments can often solve a problem before it arises, and changes in water chemistry may call for a different type of resin.
Some media (such as acid neutralizers) are sacrificial, meaning they dissolve in the water. Media used in a backwash filter are not sacrificial but will lose filtration capacity over time. When this happens, they need to be replaced with new resin. Some widely used filtration media include:
- Birm: lightweight catalytic filter for removing iron and manganese through aeration.
- Carbon: treats for taste, odor, chlorine, VOC’s and the removal of organic particles
- Filter-AG: Comprised of quartz and silica, a lightweight, irregularly shaped media for removal of suspended matter and turbidity.
- Granular Activated Carbon (GAC): High grade catalytic carbon for the removal of chlorine and chlorine by-products, chloramine, hydrogen sulfide, and general chemical reduction including herbicides and pesticides
- Katalox Light: Advanced filtration media composed of naturally minded ZEOSORB, magnesium dioxide and hydrated lime, used for removing iron, manganese and hydrogen sulfide; treats for taste and odor
- KDF: Primarily composed of copper and zinc particles designed to reduce water soluble heavy metals, iron, hydrogen sulfide, and chlorine (not as effective as carbon/GAC for removing chloramine)
- Manganese Greensand: charcoal media used to remove iron, manganese, hydrogen sulfide, arsenic and radium
- MTM: a granular manganese dioxide filtering media for treating iron, manganese and hydrogen sulfide (must be regenerated with potassium permanganate)
Reverse Osmosis Filter & Membrane Cartridge Replacement
An EcoWater Reverse Osmosis drinking water filtration system provides safe, high quality drinking water right from your kitchen sink. More convenient and less expensive than bottled water, your EcoWater R/O will pay for itself over time and costs just pennies a day to operate. Adhering to our annual maintenance program ensures a continual supply of worry-free, high quality drinking water.
Every year, replace pre and post filters:
- The prefilter removes sediment, particulate matter, chlorine taste and odor.
- The post filter is an activated carbon absorption block that further removes taste and odor, polishing the water before introducing it to your sink.
Every 3 years, replace semi-permeable membrane:
- When water is forced through the semi-permeable membrane a high percentage of dissolved solids are captured and rejected to the drain.
Ultraviolet (UV) Disinfecting System: Replacement Lamp & Quartz Sleeve
Deactivating microbiological organisms isn’t a process you want to disrupt when it comes to your water supply. Luckily, maintaining your ultraviolet (UV) disinfection system is relatively easy. There are only two components that require yearly replacement:
- The UV Lamp: if your UV system is in continual use, the UV lamp should be replaced annually. Over time, germicidal UV-C decreases and the lamp becomes increasingly less effective at deactivating microorganisms.
- Quartz Sleeve: the quartz sleeve protects the UV lamp from touching the water and is responsible for transmitting UV light into the water. When the sleeve becomes fouled or cloudy from mineral deposits, it’s no longer delivering a full UV dose.
Note: If your UV disinfection system is installed in a seasonal or second home and is not in continual use, they may require less frequent replacement.
Because sediment or particles in water can hide bacteria in any UV system, it is always suggested that a UV system follows some form of pre-filtration.
Radon Mitigation Unit Annual Service
Because of the health risks associated with radon in drinking water, it’s important that you maintain your radon mitigation unit. With an annual service plan you can rest assured that if your system malfunctions any time between service calls, Summit View Water Ltd is committed to resolving your problem and getting your system back up and running. Since your Bubble-Up Interactive Meter Control will automatically remind you when it’s due for routine maintenance, there’s no need to worry. Annual service to your Bubble-Up or Bubble-Up Junior includes:
- Check the operation of the float, pump control, and blower
- Clean and rebuild solenoid valve
- Check incoming flow rate on meter control
- Inspect vent line outlet
- Check that the motorized ball valve is operating correctly
- Replace battery in water alarm valve control
- Inspect both float switches, low water and fill
Arsenic Tank Swap
If your well water contains arsenic, you definitely want to know that your arsenic removal system is doing its job. Since arsenic is colorless, odorless and tasteless, how will you know? Our npXtra arsenic removal system by R.E. Prescott is designed to provide proof that your system is working consistently and correctly. After installation and warranty registration, sample kits containing pre-paid, pre-addressed return labels are automatically sent to you for ongoing testing. With easy to follow instructions, you simply fill three sample bottles from three sample valves and return them at prescribed intervals. A state certified, third party testing lab will analyze the results. As a 2-tank system, the npXtra is designd to provide you with extra insurance against arsenic contamination. When testing concludes that the first tank is exhausted, the second tank is still protecting your water. At that time, a tank swap is made for continued peace of mind.
DIY
We offer a full line of replacement products for the do-it-yourselfer. If you hit a snag along the way, we’re here to help.